ATTIC - INTRODUCTION
In heating climates, anywhere between 10% and 15% of a buildings total heat loss can be through the ceiling into the attic. Half (50%) of this heat loss is by conduction, which is heat flowing right through the attic insulation and framing. Air leakage through tiny holes, openings and cracks accounts for the remaining 50% of the heat loss, as well as being the cause of attic condensation and moisture build-up problems. The importance of effective air sealing cannot be overstated.
High insulation levels (R-values) in ceilings or attics (*) are recommended in almost all cold climate housing guidelines. As these areas are usually easily accessible, with few obstructions, it is here that extra insulation is usually added. Walls and other areas of the house tend to be over-looked, due to the high cost of upgrading the insulation in sealed and finished assemblies. The truth is, that other areas such as unfinished basements and uninsulated walls will typically lose more heat than the attic. The reason is that even though warm air rises; heat always travels toward the coldest area regardless of direction.
In houses with attics, the cost to increase insulation levels is only the additional material and installation costs. Houses with cathedral ceilings are more complex to insulate and have an increased cost compared to standard attics, but are still far less expensive to upgrade than wall insulation levels. Higher insulation levels accomplish two things, first, it reduces winter heat loss through the ceiling to a minimum level and secondly, it greatly reduces summer heat penetration from the attic into the home interior, thereby reducing overheating and summer cooling loads.
There are four main factors to be considered when insulating attics or roofs;
- Framing structures must allow space for adequate insulation plus room for ventilation above the insulation.
- Framing should allow for the full thickness of insulation to be applied over the exterior wall top plates.
- The insulated ceiling needs a properly installed air/vapour barrier under the insulation which must be sealed airtight.
- Proper attic ventilation is required to remove any moisture buildup and help to reduce summer heat buildup.
(*) Recommended levels for ceiling R-values with standard construction (R-12 to R-20 [RSI 2.11 to RSI 3.5] wall insulation) are R-34 to R-40 (RSI 6 to RSI 7.05). Recommended ceiling insulation levels for super insulated homes (higher than R20 [RSI 3.5] wall insulation) are R 60 (RSI 10.5).
Check local building codes for insulation and ventilation requirements for your area.
ATTIC - INSULATION MATERIALS
Batt Insulation
Glass Fibre
Glass Fibre Batts are manufactured from glass which is spun into long fibres, then woven and coated with a binding agent. Batts are light weight, fit standard joist and stud spaces and if installed carefully will not slump or settle. They do not, however, readily fit into irregular spaces and can leave 'insulation voids' around obstructions (nails, electrical wires, trusses, etc.). During installation glass fibre can cause eye, skin and respiratory irritation and manufacturer's safety
recommendations should be followed. Average R-value is 3.2 per inch (RSI .022/mm).Advantages
- Manufactured for standard joist and stud spacings
- Relatively easy to install
- Fire and mold resistant
- Small amounts of moisture have little effect on R-value
Disadvantages
- Can cause eye, skin and respiratory irritation during installation
- Does not readily fit into irregular spaces
- Can leave 'insulation voids' around obstructions if care is not taken during installation
- Air movement around the insulation can significantly degrade R-value
- Should not be covered with heavier insulation or other materials which may compress it
Mineral Wool (Slag and Rock Wool)
Mineral Wool is manufactured from melted industrial slag, which is fiberized and treated with oil and binders to suppress dust and maintain shape. It is similar to glass fibre in texture and appearance. Rock Wool is manufactured in a similar manner except that natural rock is used instead of slag. These materials have a high fire resistance but can cause eye, skin and respiratory irritation during installation.
The average R-value for both slag and rock wool batts is 3.3 per inch (RSI 0.023).
Advantages
- Manufactured for standard joist and stud spacings
- Relatively easy to install
- Good material for insulating around chimneys, since it doesn't support combustion
- Small amounts of moisture have little effect on R-value
Disadvantages
- Can cause eye, skin and respiratory irritation during installation
- Should not be covered with heavier insulation or other materials which may compress it
- Does not readily fit into irregular spaces
- Can leave 'insulation voids' around obstructions if care is not taken during installation
Loose Fill Insulation
Cellulose Fibre
Cellulose fibre insulation is made from finely shredded newsprint which is chemically treated to resist fire and fungal growth. Due to the small size of the particles, cellulose can 'flow' around obstructions (nails, electrical wires, trusses, etc.) to give a uniform fill.
Blown Cellulose has an average R-value of 3.6 per inch (RSI
0.025/mm) which is dependant on the chemical, paper type and it's blown density. If the insulation is not blown to manufacturer's recommended density it can settle over time, and the intended R-value will not be obtained.Poured Cellulose has an average R-value of 3.4 per inch (RSI 0.024/mm) and must be applied to the manufacturer's recommendations to achieve desired density and R-value.
Advantages
- Fills irregular horizontal spaces
- Blown-In Cellulose can be installed with rented equipment or hand poured
- Chemical additives provide fire, corrosion, vermin and fungal growth resistance
- Small amounts of moisture have little effect on the materials R-value
Disadvantages
- Should not be covered with heavier insulation or other materials which may compress it
- Will settle over time, manufacturer's recommendations should be followed to achieve desired
R-value- Will compress and harden if subject to high moisture levels
Glass Fibre
Blown Glass Fibre is a similar material to glass fibre batts, except that the material is 'chopped up'. It has an R-value of 2.9 per inch (RSI 0.02/mm), which is reduced if it is not blown to the proper density. The particles in glass fibre tend to be larger than those in cellulose, therefore it doesn't always flow as freely around obstructions and can leave insulation voids. As with the batts, during
installation glass fibre can cause eye, skin and respiratory irritation and manufacturer's safety recommendations should be followed.Poured Glass Fibre has basically the same properties as the blown product except its R-value is usually slightly higher, R-3 per inch (RSI 0.021/mm).
Advantages
- Fills irregular horizontal spaces
- Small amounts of moisture have little effect on the materials R-value
Disadvantages
- Can cause eye, skin and respiratory irritation during installation
- Should not be covered with heavier insulation or other materials which may compress it
- Can settle over time if not blown properly, (manufacturer's recommendations should be
followed)Mineral Wool (Slag and Rock Wool)
Mineral Wool is manufactured from melted industrial slag, which is fiberized and treated with oil and binders to suppress dust and maintain shape. It is similar to glass fibre in texture and appearance. Rock Wool is manufactured in a similar manner except that natural rock is used instead of slag.
The properties listed below refer to both types of insulation.
The blown material has an R-value of 2.7 per inch (RSI 0.019), and as with all blown materials this will vary depending upon the installed density. These types of materials have a high fire resistance but can cause eye, skin and respiratory irritation during installation.
The poured material has the same characteristics as the blown material, but with a slightly higher R-value, R-3 per inch (RSI 0.021). Manufacturer's recommendations should be followed for installation techniques.
Advantages
- Good material for insulating around chimneys, since it doesn't support combustion
- Fills irregular horizontal spaces
- Small amounts of moisture have little effect on the materials R-value
Disadvantages
- Can cause eye, skin and respiratory irritation during installation
- Should not be covered with heavier insulation or other materials which may compress it
- Can settle over time if not blown properly, (manufacturer's recommendations should be
followed)Vermiculite
Vermiculite is a mineral closely related to mica, which when heated, expands to form a light weight material with insulating properties. There are two types of vermiculite: untreated and treated. The treated material is coated with asphalt to make it water-repellent for use in high moisture areas. Untreated vermiculite absorbs water, and once wet, dries very slowly.
Untreated vermiculite has an R-value of 2.3 per inch (RSI 0.016/mm) compared to R-2.5 (RSI 0.017) for the treated material. Vermiculite is usually hand-installed, and is suitable for both horizontal and vertical applications. It is non-combustible, odourless and non-irritating, although due to its high density it is not usually the material of choice where a high R-value is desired.
Advantages
- Pours easily into irregular spaces
- Non-combustible
- Non-abrasive, odourless and non-irritating
Disadvantages
- Dries very slowly after absorbing moisture
- Not usually used where high R-value desired
Wood Shavings
Wood shavings, although rarely used today, were once a very popular insulation product due to their wide availability and low cost. Shavings were often treated with lime or other chemicals, to increase resistance to water absorption, fire and fungal growth. This insulation product is still a common sight in older homes across North America.
Wood shavings have an average R-value of 2.44 per inch (RSI 0.0169/mm). They tend to absorb moisture and dry very slowly. Over time the material may settle and is hard to effectively treat against fire, vermin and fungal growth.
Advantages
- Readily available and inexpensive
Disadvantages
- Low R-value
- Dries very slowly after absorbing moisture
- Hard to effectively treat against fire, vermin and fungal growth
- Can settle over time
ATTIC - VENTILATION
There are three traditional reasons for ventilation of an attic or roof space.
1. The first is ventilation to control humidity and minimize condensation on the attic or roof framing, sheathing and insulation.
The concept is that air flow through the attic or roof cavity will remove any excess moisture build-up. In theory this sounds good, but in reality, the air moving through the attic or roof cavity, during the heating season, is cold and can hold very little water vapour.
As long as interior air leakage into the attic or roof cavity is small, standard ventilation should control moisture build-up. If a moisture problem is evident in the attic or roof space, it is usually more effective to seal any leaks in the air/vapour barrier than to increase ventilation in the attic. The best method for
reducing condensation or moisture problems in any roof or attic space is to prevent water vapour from entering in the first place.
Typical Attic Air Leakage PointsListed as an example are the current ventilation requirements for the Canadian National Building Code.
- 1 (one) square foot of venting for each 300 square feet of ceiling area, for roofs over 1 in 6 slope.
- 1 (one) square foot of venting for each 150 square feet of ceiling area for roofs under 1 in 6 slope.
- Of the total venting, 50% should be soffit venting and 50% roof, gable or ridge venting, equally distributed on opposite sides of the roof to ensure good cross-ventilation. Figures are based on free ventilation area, blockage created by screens or louvres must be accounted for.
Check your local building code for ventilation requirements in your area.
In Northern Canada, fine particles of wind blown snow can infiltrate into the attic and roof spaces creating moisture problems. Most types of roof and gable vents are quite susceptible to this problem. Since 1988 the Northwest Territories Housing Corporation (Canada) has been building sealed, unvented standard and cathedral roofs without any major moisture problems. This type of roof is now standard for all Public Housing units north of the tree line. Unvented or "hot roofs", are currently not permitted in the Canadian National Building Code except in the North West Territories.
2. The second is that ventilation will improve the life expectancy of roofing materials by reducing roofing and roof sheathing temperatures in summer.
The concept here is that ventilation will reduce summer surface temperatures of roofing materials and extend the usable life span. It is true that higher operating surface temperatures can greatly reduce the service life of roofing materials. Unfortunately, traditional physics and current evidence shows that ventilation is not effective in lowering surface operating temperatures. Operating surface temperatures of roof membranes, shingles and sheathings are far more dependant on
colour, orientation, solar intensity and wind exposure than on attic or roof ventilation.3. The third is that ventilation will reduce cooling loads and increase occupant comfort levels during the cooling season. With a poorly insulated (less than R-10) attic or roof assembly, ventilation can reduce cooling loads by as much as 25%. Ventilation however, has little or no effect on the cooling loads of attic or roof assemblies with R-25 or greater insulation levels.
Conclusions
- The best way to reduce condensation or moisture problems in an attic or roof assembly is to eliminate interior air leakage through the ceiling with a properly installed air/vapour barrier and proper air sealing. Ventilation must still be provided, but at the minimum level allowed by local building codes.
- Ventilation does not extend the life of roofing membranes or shingles. Lighter coloured roof membranes and shingles have much longer service lives because they have a lower surface operating temperature.
- The most effective method for reducing cooling loads is not to increase ventilation. Light coloured roofing membranes or shingles combined with good insulation levels and a well sealed air/vapour barrier will reduce cooling loads more effectively.
ATTIC - TYPES OF ATTIC VENTS
Roof or attic vents should be located to allow good cross ventilation from end to end and top to bottom if possible. Vents should be equipped with screens to keep out pests and bugs and louvres to keep out rain and snow. Some of the different types of roof vents are listed below.
- Soffit-Vents:
- A continuous screened vent usually installed on the underside of the eaves. Soffit venting is most effective when combined with ridge, gable end or passive roof vents.
- Gable End:
- These vents are usually installed at the peak of the gable ends on opposite sides of the roof. Works best when combined with soffit-venting.
- Ridge Vents:
- This is a continuous vent applied to the entire length of the roof ridge. Works best when combined with soffit-venting.
- Roof Vents:
- Passive roof vents come in a variety of shapes and sizes. These vents can be installed both high and low on the roof to provide top to bottom ventilation or with other types of roof vents for cross ventilation.
- Turbines:
- Turbine ventilators are louvred spinning balls attached to a solid base. As warm air rises through the vent it causes the turbine to spin which in turn draws more air out of the roof or attic cavity. This action also occurs in windy conditions both in summer when needed and in winter. When combined with continuous soffit venting these units work well but there is a potential for turbine ventilators to create negative pressures in attics with limited air supply. This can create a potential moisture problem (interior moist house air drawn into the attic or roof cavity by negative pressure) during the winter in heating climates.
- Power Vents:
- Usually controlled by a thermostat, these units use powered fans to exhaust air out of the attic or roof cavity to provide cooling. From the view point of energy efficiency operating costs or potential problems these types of vents are not recommended for residential use.
ATTIC DETAILS
This series of details shows various techniques for air sealing, insulating and ventilating a typical attic space.
- Sealing Attic Penetrations
- Sealing Attic Penetrations II
- Insulating The Attic Space
- Air Sealing A Recessed Light Fixture
- Sealing The Attic Hatch
- Installing Batt Insulation
- Types of Attic Ventilation
- Raised Heel Truss
- Cantilever Truss
SEALING ATTIC PENETRATIONS

Metal plumbing stacks are difficult to seal well, due to the expansion and contraction that occurs as warm air flows through them. The most effective way to seal a stack with no expansion joint is shown in this detail. Heavy polyethylene is sealed to the stack using duct tape (or a pipe clamp) and to the ceiling finish with acoustical sealant and staples.
Polyethylene cannot be used to seal around chimneys. Instead, heat resistant sealant (muffler cement) is used to seal any gaps. For wide gaps, gypsum wallboard can be used as a backing for the sealant. Due to possible fire hazards, insulation must not come any closer than 2 inches (50mm) to the chimney. Batt insulation can simply be cut to the required length, however loose fill insulations should be held back with a metal or gypsum wallboard barrier (insulation stop).
Wiring penetrations through the ceiling air/vapour, can be sealed using caulking. Caulking can also be used to seal any gaps along the top plates of interior or exterior walls. Polyurethane foam should be used for gaps which exceed 1/2 inch (12mm) in width.
SEALING ATTIC PENETRATIONS II

This detail shows a plumbing stack with an expansion joint, the stack is sealed to the ceiling finish using a tight-fitting plywood plate and caulking.
Polyethylene cannot be used to seal around chimneys. Instead heat resistant sealant (muffler cement) is used to seal any gaps. For wide gaps, gypsum wallboard can be used as a backing for the sealant. Due to possible fire hazards, insulation must not come any closer than 2 inches (50mm) to the chimney. Batt insulation can simply be cut to the required length, however loose fill insulations should be held back with a metal or gypsum wallboard barrier (insulation stop) which must extend 3 inches (75mm) above the insulation, and not closer than 2 inches (50mm) to the chimney itself.
Electrical boxes which penetrate the ceiling air/vapour barrier should be sealed using heavy polyethylene which is caulked and stapled, or from the interior of the house using suitable foam gaskets.
INSULATING THE ATTIC SPACE

Heavy polyethylene is placed over and between the ceiling joists (if no air/vapour barrier is present), being sure that it fits snugly into the spaces and that all joints are overlapped and caulked using acoustical sealant.
The batts are fitted tightly together between the joists, with care taken to extend the insulation as far as possible over the top of the exterior wall without cutting off the air flow from the soffit vents (insulation stops can be installed between the rafters to keep the vents open). Subsequent layers of batt insulation should be run in opposite directions, to help reduce heat loss through the joists and joist spaces.
If loose-fill insulation is used, it can be poured or blown into place, and a rake or screed board used to level it off.
AIR SEALING A RECESSED LIGHT FIXTURE
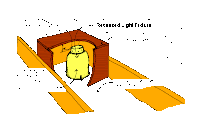
Lights which are recessed into the attic cavity, should not be directly covered with insulation as they need an adequate air space around them in order to prevent heat build-up when the light is in use. A 1/2 inch (12mm) plywood or gypsum wallboard box can be constructed to surround the fixture and provide the air space it needs. The fixture should not be closer than 1 inch (25mm) to any side of the box and not closer than 6 inches (150mm) to the top. The box should then be covered with heavy polyethylene, which is caulked, using acoustical sealant, to the ceiling surface.
Note: The most efficient solution would be to replace any recessed fixtures with standard ceiling fixtures, and then to seal the old penetrations using polyethylene and caulking.
SEALING THE ATTIC HATCH

The attic hatch should be treated exactly as any exterior door. Place weatherstripping along the casing or the edges of the access door. Caulk around the frame, and between the casing and the ceiling finish. A latching mechanism should then be added (hooks with eye bolts, etc.) to ensure that the hatch seals tightly against the weatherstripping. On the attic side, the hatch should be insulated, rigid insulation usually works well in this area.
Note: When an attic hatch is required in new construction, it should, whenever possible, be located outside the thermal envelope of the house, such as through a gable end.
INSTALLING BATT INSULATION

Batt insulation is relatively simple to install, and is effective if care is taken and a few simple rules are followed.
- Butt the ends of the batts together as snugly as possible.
- The first layer of insulation should fill the joist space completely, so that the second layer can run perpendicular to the first, preventing heat loss through the joists.
- Ensure that subsequent insulation layers sit tightly together, and that no air gaps exist between them.
- The insulation should be extended over the top plates of exterior walls, and insulation stops used to prevent it from blocking air flow from soffit vents.
- Irregular shaped spaces/gaps should be insulated with custom cut pieces or loose fill insulation.
TYPES OF ATTIC VENTILATION
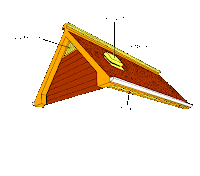
This detail shows the most common types of attic ventilation. Vents should be located to ensure a good cross ventilation, from end to end, and from top to bottom of the attic cavity. Local building codes should be consulted for the ventilation standards for your area.
RAISED HEEL TRUSS

The raised heel truss is designed so that a full depth of insulation can be added at the attic perimeter (exterior walls). Heat loss through the top plates of exterior walls can lead to serious problems in cold climate areas, (ie. ice damming), making the full depth insulation an important factor. These benefits can out-weigh the additional costs associated with this type of truss.
CANTILEVER TRUSS
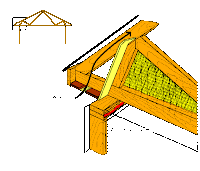
The cantilever truss is designed so that a full depth of insulation can be added at the attic perimeter (exterior wall), however, depending on the roof slope, and the projected length of the cantilever this may not always be the case.
1 comment:
Our condo trustees are considering adding gable hatches to our buildings, so we can make periodic inspections without disturbing our owners, each of whom has a hatch in their upstairs linen closet.
Do you have any recommendations on suppliers of pre-fabricated hatches, or are we left to our own designs?
Post a Comment