INTRODUCTION
This section is designed as a guide to understanding, energy efficient house construction. The Canadian 'House as a System' planning approach was used. This approach ensures that all of the components which make up the home function well together.
Energy efficient housing is not any particular housing style or type, almost any housing can be built using energy efficient construction techniques. Improvements in design and construction which lower energy use are permanent and are one-time-only costs which increase the value of your home, while lowering the ongoing operating costs.
Energy efficient housing in simple terms is 'housing which uses the energy put into it as efficiently as possible'. It is not difficult to plan and build energy efficient housing. Using existing techniques and materials, total home energy usage can be reduced by 60% to 80%.
The extra costs for upgraded materials, construction, insulation and airtightness required for energy efficient housing should only add 5% to 10% to the total building cost. With potential savings of 60% to 80% on energy costs, the simple payback period may only be 5 to 8 years at current energy costs. Simple payback is calculated by dividing the increased building cost by the yearly energy cost savings.
Faced with today's ever increasing cost of energy, and concern over what future energy costs will be, building energy efficient housing makes more economic sense now than ever. Energy efficient housing uses less energy and therefore produces less pollutants, this is one area where each of us can help preserve the environment for future generations.
Energy Efficient Construction
The basic shell construction assemblies of a home - foundation, walls, floors and roofs - are covered in detail in this section. Standard house building practices are illustrated with the emphasis on high insulation levels and a continuous air/vapour barrier installation. Details include how the floor, wall and ceiling assemblies join (and the sealing problems created) and how airtightness and insulation levels are maintained in spite of obstructions such as windows, doors, wiring, plumbing, pipes, or chimneys. The object is not to cover all aspects of structural building design - only how energy efficient construction can be incorporated into existing residential construction practices.For reference, Table 2 lists metric building material sizes along with Imperial equivalents.
Controlling Heat Loss
Most important to the success of an energy efficient home is the quality of construction. Even poorly sited homes (as often occurs in urban areas), with little passive solar gain potential, can be very energy efficient homes. Adequate levels of insulation and careful sealing can combine to cut heat losses so that the energy required for space heating will only be 15% to 25% of a 'normally' constructed home.

A good way to think about a house is to consider it a 'shell' which must keep heat inside during the winter. This shell is made up of floors, ceilings and walls constructed with various building materials. Heat is lost from the inside of your home in two ways: either directly through the shell or when warm indoor air leaks out through cracks and holes (replaced by cold outside air leaking in).
Energy loss through the building shell can be 40% to 70% of the total and is controlled with insulation. Air leakage losses account for the remainder and is controlled by the air/vapour barrier, weatherstripping and caulking.
Insulation
Insulation is measured by its R-value (or RSI-value). The higher the R-value, the better the insulation stops heat flow. R-values for different building materials are given in Table 1. The total R-value for a wall, ceiling or floor is the sum of the values of each part or layer.
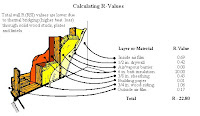
For an Energy Efficient House in a cold climate (5000 heating degree days or less), the recommended R-values (RSI-values) are:
- R-10 (RSI 1.7) under foundation floor.
- R-30 (RSI 5.0) for above grade floors such as overhangs, cantilevers and below projecting windows.
- R-20 (RSI 3.5) for all walls above and below grade.
- R-40 (RSI 7.0) for all ceilings whether sloped or flat.
For a Super Energy Efficient House in a cold climate or if building in a very cold climate (5700 heating degree days or more), the recommended R-values (RSI-values) are:
- R-30 (RSI 5.3) for all foundation walls.
- R--36 (RSI 6.3) for all walls above grade.
- R-40 (RSI 7.0) for above grade floors such as overhangs, cantilevers and below projecting windows.
- R-60 (RSI 10.5) for all ceilings whether sloped or flat.
Most insulation products can be placed in one of three types - blanket, loose fill or rigid.
Blanket Insulation (often called 'batt') is the easiest to handle and being premanufactured, has a consistent quality. It is most suitable for application to vertical cavities (as in walls). There are two common kinds, glass fibre and mineral fibre, both with an R-value of about R-3.5 per inch (RSI-value 0.024 per millimetre)
Loose Fill Insulations are made from a variety of products and all work well for horizontal surfaces such as ceilings where the depth is not a problem. They can also be used in regular or irregular joist and wall cavities. It is essential that loose fill materials made of wood or paper products be treated for fire resistance. R-values range from R 2.5 to 3.5 per inch (RSI-values 0.016 to 0.024 per millimetre of thickness).
Rigid Insulations are made of a number of products such as polystyrene, fibreglass, urethane or isocyanurate. They are the most expensive types but do offer the highest R-values up to R-7.5 per inch (RSI-values to 0.051 per millimetre). Rigid insulations are a fire hazard when exposed to the interior but are considered safe when installed properly. In particular, they can be used on the interior of a home if covered by at least 1/2 inch (12 mm) of drywall or plaster which is mechanically fastened to the structure. Rigid insulations can be used on the outside of concrete, masonry or wood walls and under siding or stucco finishes. Some high density types are suitable for use under concrete floor slabs.
Spray-Foamed Insulations are mixed on the job site by the contractor/ installer. A liquid type foam is sprayed directly into wall cavities. The foam expands in place and sets in a short time span. Installation should only be handled by qualified installers. R-values range from R-3.5 to 6.0 per inch (RSI-values 0.024 to 0.042 per millimeter of thickness).
Sprayed-in-Place Insulations are loose fill products which are blown in to wall cavities. A mesh or plastic film is attached to the walls, the insulation is then mixed with an adhesive, usually water-based and then blown into the wall cavities. The three most common types of insulation installed in this way are cellulose, glass fibre blowing wool and mineral or rockwool. R-values range from R-3 to R 3.5 per inch (RSI-values 0.024 to 0.032 per millimetre of thickness).
The proper choice of insulation type depends on its use. In addition to high thermal resistance, a good insulation should have low absorption of water, resistance to fire, bacteria and vermin, reasonable cost, and be easily applied.
Air Leakage
The air/vapour barrier plays the most important role in controlling air leakage heat losses and, in conjunction with caulking and weatherstripping, creates the seal between inside and outside. Exterior air barriers (taped) are recommended under any exterior siding or finish materials which are subject to air penetration
Caulking is used to seal any gaps where two surfaces meet but have limited or no movement. Most types of caulking will 'skin over' so they can be painted or are not sticky to touch when hardened.
- Oil or resin based caulks are inexpensive, but are not very durable (less than 5 years).
- Latex based materials are reasonably priced and durable, as well as being applicable to a number of different situations.
- Butyl rubber compounds are expensive but work the best for sealing wood to concrete surfaces (should only be applied in well ventilated areas).
- Elastomeric caulks (silicone and polysulphide) are very expensive but also very durable.
- Acoustical sealant, does not harden or form a skin and is used for sealing joins in the air/vapour barrier.
- Polyurethane foam is a special type of material useful for sealing large gaps around rough openings or along sill plates.
Weatherstripping is used to control air leakage at joints where two surfaces meet and move such as opening windows and doors. Weatherstripping is available in compression types, wedging types and magnet types. Good quality windows and door units are supplied with quality weatherstripping materials and are tested for air leakage rates. One should select units which have been tested and shown to have air leakage rates of less than 1/2 cfm per foot of sash length (0.80 litres per second per metre).
Polyethylene sheets are used for the air/vapour barrier. It is essential, in an energy efficient house, that the air/vapour barrier be continuous and all joints between sheets be sealed over solid backing. A non-skinning caulking such as acoustical sealant is used to seal between joints in the polyethylene. Because polyethylene is often handled roughly when being installed, 6 mil thick (0.150mm) sheets should be used. In addition to being more fragile, thinner polyethylene is much more permeable to air/vapour transmission than the thicker 0.150mm (6 mil) sheets.
The air/vapour barrier has another role to play in house construction. In addition to controlling air leakage, it prevents water vapour movement into the walls, ceilings or floors.

If vapour from the interior is allowed to enter an insulated assembly during cold weather, it could condense and form ice at some point in the wall. When the ice melts, deterioration of the insulation and structural components will occur over time. There is also a potential for supporting mold growth within the wall assembly which can cause indoor air quality problems. For this reason, the air/vapour layer must be located near the warm (or interior) side of ceilings, walls and floors.
Research has shown that as long as the air/vapour barrier is placed within the first one-third of the total assembly R-value (measured from the warm side), then no condensation problems will occur.
Foundations
Every building must have an adequate foundation to support it. In cold climates, foundations usually form an enclosure under a building - a crawl space or basement - although some (slab-on-grade) are built right on the ground. Controlling the heat loss through the foundation is very important. Contrary to popular belief, earth is not a good insulator and one-third of the total heat loss in a home can occur through an uninsulated basement.
Masonry or Concrete Foundation Walls
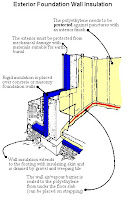
Cast-in-place concrete or block-type walls are the most commonly used in Canada. Insulating this type of foundation is best done on the outside if possible. The large amount of thermal mass in a masonry or concrete foundation is included in the interior volume of the house if it is insulated on the outside. As well, the foundation is less susceptible to frost damage and leaking. Rigid insulation or glass fibre sheets can be used. The above grade portion must be protected with stucco, treated plywood or similar rigid exterior finishes. Since masonry or concrete walls are quite porous, a polyethylene air/vapour barrier is added on the interior to eliminate any potential condensation problems with the completed interior walls. The exterior foundation insulation details shows the application of rigid insulation.

Most masonry foundations however, have been, and will continue to be insulated on the inside. A most important step is placing a moisture barrier of polyethylene on the inside of the wall from the exterior grade level to the floor. The wall interior is then insulated and sealed similar to frame wall construction. It is also possible to use rigid insulation, attach an air/vapour barrier, then finish the wall directly over it. The interior finish is difficult to attach through the rigid insulation - which must be 4 to 6 inches thick (100mm to 150mm) in order to have an R-20 value (RSI 3.5). If plastic rigid insulation is used, drywall which is mechanically fastened to the foundation wall must cover it. A 2 x 4 inch (38 x 89 mm) stud wall frame work spaced 1.5 inches (36mm) out from the foundation wall, as illustrated, can be insulated with R-20 (RSI 3.5) batt-type insulation products.
This provides the easiest and most economical route if a foundation wall must be insulated on the inside. The interior foundation insulation detail shows how this is best done to provide a well-sealed and insulated wall.
There are currently a number of products available from manufacturers which offer rigid interior foundation insulation systems. These systems each have their own methods for attaching both the insulation and the interior finish and offer an effective alternative to wood framing and batt insulation.
Pressure Treated Wood Foundation Walls

Wood foundations can easily be made very energy efficient. Often called a 'PWF' foundation they can be constructed in almost any type of weather. A wood foundation must, however, be designed by a qualified engineer and constructed by competent builders who understand the importance of proper base preparation, handling techniques for pressure treated materials, the use of correct fasteners, drainage installation, backfilling techniques and sealing requirements. Because the foundation walls are an extension of typical wood frame construction, installing batt insulation and applying the air/vapour barrier is quite straight forward.
PWF Foundation Floors

The floor in a pressure treated wood foundation can be a concrete floor slab. Rigid Insulation should be placed under the foundation floor to a minimum insulation level of R-10 (RSI 1.7). A moisture barrier of at least 6 mil polyethylene (overlap seams) is required. A 3 to 4 inch (75 to 100 mm) layer of sand placed on top of the rigid insulation and the air/vapour barrier protects both during the floor pour and aids in proper concrete curing. Extra insulation to protect footings may be required for shallow footing depths as is often the case in bilevel or crawlspace foundations.
The floor in a pressure treated wood foundation can also be constructed of pressure treated wood. Pressure treated wood foundation floors are constructed using standard floor framing techniques on a gravel drainage bed. The installation of an effective moisture barrier on top of the gravel drainage layer is very important (minimum 6 mil polyethylene sheeting with overlapped and sealed seams).The floor joist cavities can then be filled with standard batt, blown or loose fill insulations. An air/vapour barrier is then installed on top of the floor joists. The attachment of the floor and wall polyethylene sheets is another important step in creating continuity of the air/vapour barrier. Standard floor sheathing and finishes can then be applied.

Polystyrene Foundation Walls
There are two basic techniques used to construct foundation walls using rigid polystyrene insulation. Some systems offer either polystyrene blocks or panels which use concrete and steel reinforcing placed into the cavities for structural support.
Other systems offer solid polystyrene panels using metal or wood studs for structural requirements. In either case, an interior polyethylene air/vapour barrier is applied and covered with a fireproof layer of drywall or plaster which must be mechanically fastened to the structural part of the wall. The outside must also be covered with a rigid material or parging to protect the polystyrene from mechanical damage and degradation from sunlight and soils.

Crawl Space Construction
Many homes have been built with partial depth foundations which are often called crawl spaces. Because the crawl space area under a home usually contains some mechanical services, insulating the foundation walls and floor is recommended to keep the temperature above freezing. A crawl space floor should be treated the same as an exterior wall, insulated and sealed from the house interior space. The crawl space walls can be insulated from the interior or exterior using standard foundation insulation methods. Perimeter insulation is then added as well to ensure that the crawl space retains more heat and is able to resist frost penetration. A moisture barrier, placed over the ground surface, is necessary to keep the space dry.

As well, summer ventilation should be provided by having outside air vents into the crawl space which can be opened in spring and closed in the fall. Any accumulated moisture can then be vented out during the summer months.
Slab-On-Grade Construction
With this type of foundation the concrete slab is the combined foundation and finished floor surface. Rigid polystyrene insulation is used below the slab to lower floor heat loss. Perimeter insulation is also applied to control heat loss from the edge of the floor slab. An insulated skirt of rigid insulation extending down and away from the foundation wall around the entire perimeter will eliminate any potential frost problems, improve drainage and help further reduce heat loss.

The polyethylene air/vapour barrier can be applied on top of the insulation, directly below the slab. A 3 to 4 inch (75 to 100 mm) layer of sand on top of the rigid insulation and the air/vapour barrier will protect both during the floor pour and aid in proper concrete curing. In order to provide continuity with the wall air/vapour barrier, the floor polyethylene layer must be placed so it can conveniently join to the wall layer at some point during construction.
To better anchor a slab-on-grade foundation, it can be attached to concrete piles. Large diameter holes of 8 to 12 inches (200mm to 300mm) are drilled 10 to 12 feet deep (3m to 4m) at intervals around the edge of the foundation. Reinforcing bars tie the thickened slab edge to the piles. In soils where drainage and frost is a problem, additional piles in the centre of the foundation may be required to prevent movement.
No comments:
Post a Comment